PRODUCTION PREPARATION
Technical Office is responsible for the preparation of technical documentation and supervision of the production process.
Performed tasks:
- Analysis of the documentation for manufacturability possibilities
- Define the way to build the pattern
- Selection of the flooding system
- Determine the metallurgical parameters of the process
Elaboration of the technological process in accordance with PN-EN norms and ISO 9001:2008 instructions.
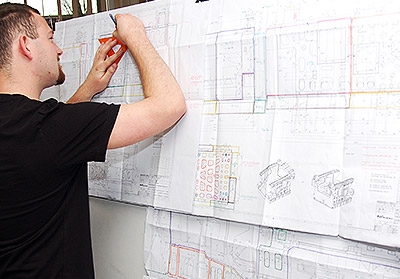
IMPLEMENTATION, MAINTENANCE AND PATTERN ADAPTATIONS
On the basis of the technical documentation the new patterns are built, other works related to the preparation pattern for production are performed (design changes imposed by the client, technological modifications, repairs and adaptations works to pattern and cores).
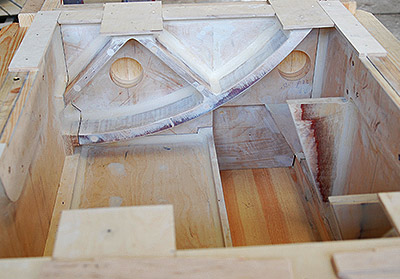
Moulding
Mold and cores are made of self-hardening furan masses.
Mass produced in a two types of mixers WSD and AMD.
The molding process used for molding boxes with dimensions: from 1000x1000mm to 8000x2000mm, and molding pits size max. 20 000 x 4000 x 2000mm.
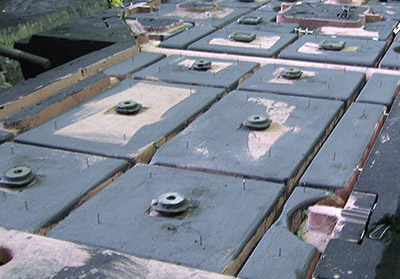
Sand reclaim AND TRANSPORT
Automated installation for the regeneration of the molding mass is used to regenerate the mass arising from the cleaning process on the shock grating .It is transported by conveyor to the tank. Mass form tank, minced, wiped from binders, dedusted and cooled to a desired temperature is fed to the regenerate tank.
Obtained in this way reclaimed mass is fed pneumatically to the molding position where it is used as a full-fledged material for production of molds and cores. We recover 96% of sand and reuse in the process of forming.
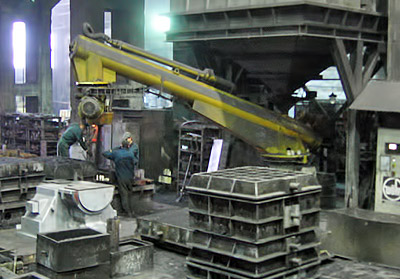
MELTING IRON
Liquid cast iron is produced in:
- OTTO JUNKER induction furnace with a capacity of 6t and performance of 8t/h
- cupola Ø1000 with a cold blast enriched with oxygen with a capacity of 8 t/h.
Molds are poured with liquid metal from tilting ladles with a capacity of up to 20,000 kg.
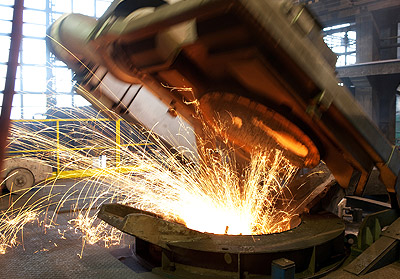
CLEANING THE CASTING
Casting are cleaned from a molding mass on a set of a shock grates. Large and complex castings are cleaned from the mass on the 160bar pressure water cleaning position. Smaller castings are shot blasted in rotation cleaners OWPK-4. Larger casts in special tent where the process of cleaning is carried out manually. At a final stage of cleaning, each castings is cleaned by hand pneumatic grinding tools.
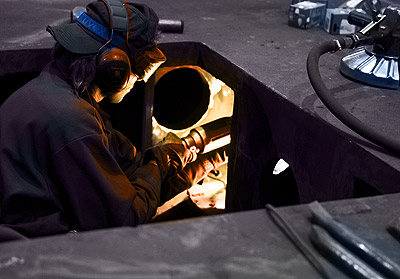
QUALITY CONTROL
Quality Control Department is responsible for overseeing the entire production process. The department carries out dimensional inspections of patterns, quality check of cores and molds, detailed dimensional inspection of the trial cast. Other tasks of the department are: testing of materials used in production process, molding mass, chemical composition and strength tests. Based on survey Quality Control Department issued material certificates, quality certificates and others certificates in accordance with the customer requirements.
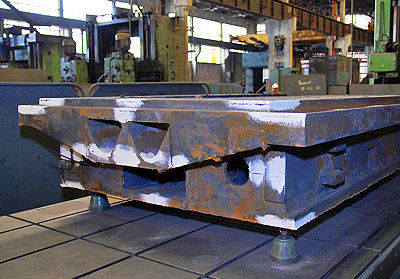
MACHINING
The process is carried out on the basis of the documentation provided by the customer. We provide machining of castings manufacture by us and castings provide by our customers. In the absence of technical capacity in the Foundry machining process is realized in the framework of the Group, using a wide range of machining of Machine Tools Factory “RAFAMET” plc.
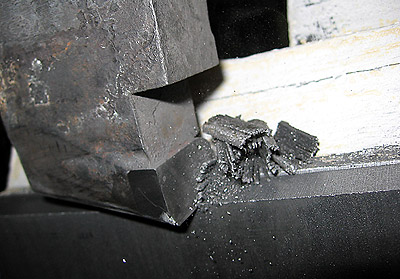
HEAT TREATMENT
Heat treatment of castings in the annealing and stabilization of casts and steel construction is carried out upon customer request. In the absence of technical capacity in the Foundry the heat treatment process is realized in the framework of the Group, using the capabilities of Machine Tools Factory “RAFAMET” plc.